ClearCalcs allows you to design a timber beam according to AS 1720.1:2010 in a few simple steps, with checks for moment capacity, shear capacity, bearing capacity and deflections.
For a basic introduction to the beam design/analysis setup, see the article ‘How to Use the Beam Analysis Calculator’.
Video Tutorial
Watch the video on How to Design a Timber Beam in ClearCalcs to AS1720.1
1. Select Beam Type
When adding a new timber beam calculation, you can select between various types of residential timber beams. The sheet and calculations for each are the same, however, some default values and criteria, such as deflection limits and centre to centre spacing, have been made specific to each beam type.
Once you have created a timber beam, you may use the change material function to quickly swap to steel, or vice versa.
![[SUPPORT]_how_to_design_a_timber_beam_to_as17201_2010_in_clearcalcs_au_0.png](https://cdn.prod.website-files.com/67189a2b26762b3b096e3184/673d7e7b0874de573c7e6765_SUPPORT_how_to_design_a_timber_beam_to_as17201_2010_in_clearcalcs_au_0_a4cea2c957.png)
2. Input Key Properties
Quick Tip - If you're ever unsure what something means in ClearCalcs,simply click the field label for references, checks, conditionals, and descriptions.
Member Selector
The member selector can be used to filter the timber sections by stress grade, or by specifying the maximum dimensions required. The selector shows a summary of the critical checks, to help you to identify the most optimal section.
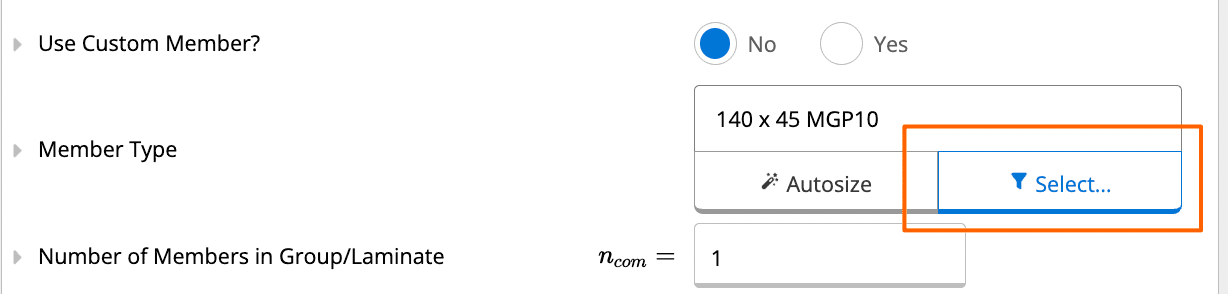
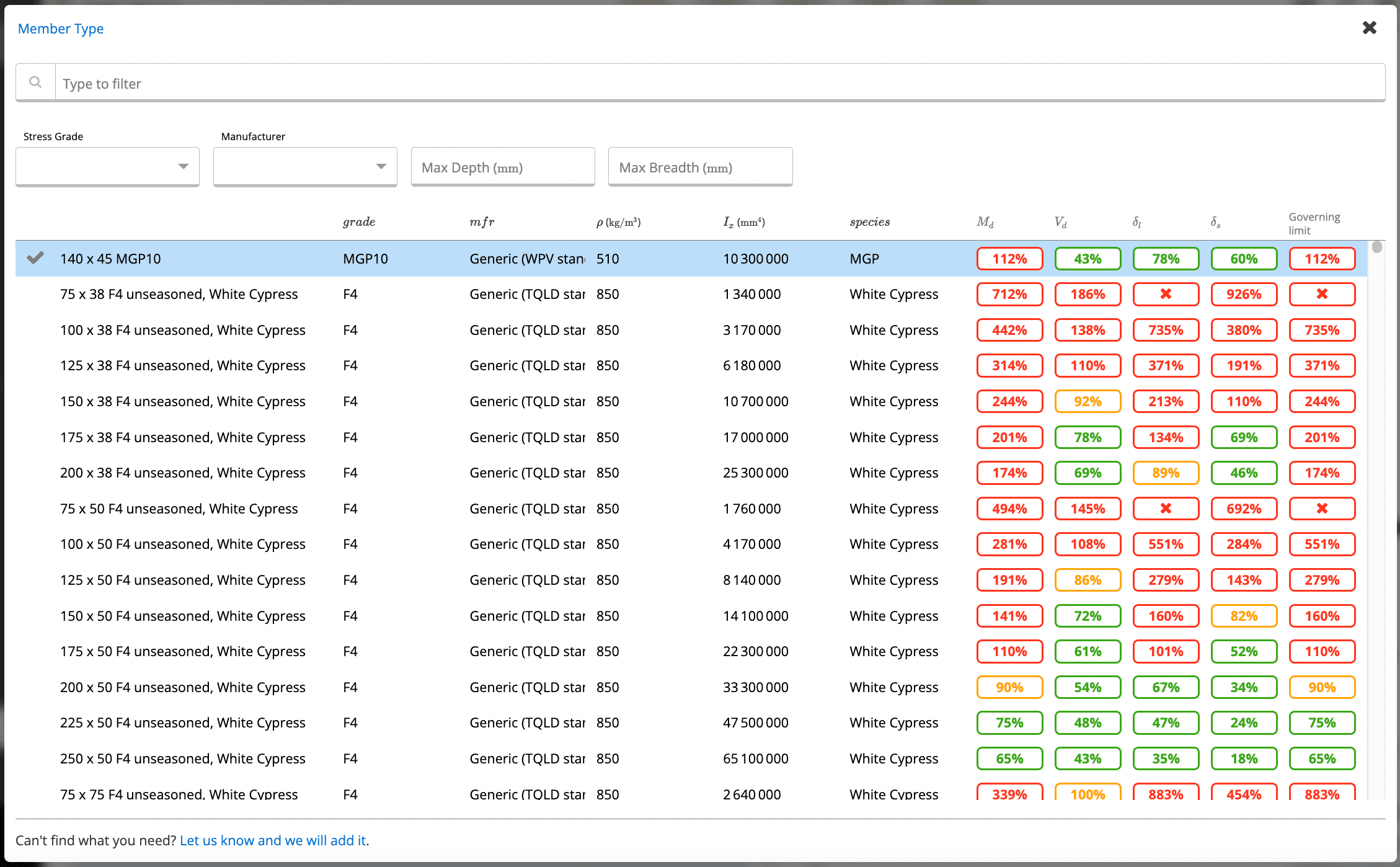
Default values have been set for other key properties, which you can modify.
Number of Members in Group/Laminate is the number of members that are nail laminated together along the depth of the beam.
Member Orientation allows you to select if the beam is loaded to bend about the major or minor axis.
![[SUPPORT]_how_to_design_a_timber_beam_to_as17201_2010_in_clearcalcs_au_3.png](https://cdn.prod.website-files.com/67189a2b26762b3b096e3184/673d7e7a0874de573c7e673e_SUPPORT_how_to_design_a_timber_beam_to_as17201_2010_in_clearcalcs_au_3_62d8482232.png)
Total Span Length is the total length of the beam, including all individual spans, in mm.
Centre-to-Centre Spacing is the distance between subsequent beams, in mm.
The Lateral Restraint Type lookup is used to determine the minor axis effective length of the beam for buckling and the slenderness coefficient, according to Cl 3.2.3.2 (e.g. see diagrams below). It depends on the spacing of restraints and whether they are at the tension or compression edge of the beam.
![[SUPPORT]_how_to_design_a_timber_beam_to_as17201_2010_in_clearcalcs_au_4.png](https://cdn.prod.website-files.com/67189a2b26762b3b096e3184/673d7e7a0874de573c7e6738_SUPPORT_how_to_design_a_timber_beam_to_as17201_2010_in_clearcalcs_au_4_6c6f7d65f1.png)
![[SUPPORT]_how_to_design_a_timber_beam_to_as17201_2010_in_clearcalcs_au_5.png](https://cdn.prod.website-files.com/67189a2b26762b3b096e3184/673d7e7a0874de573c7e6731_SUPPORT_how_to_design_a_timber_beam_to_as17201_2010_in_clearcalcs_au_5_e5a27d485a.png)
The Minor Axis Effective Length for Buckling must be input, according to the lateral restraint type (Cl 3.2.3), in mm.
The Torsional Effective Length for Buckling is only relevant for the Lateral Restraint Type “Continuous Restraints at Tension Edge with Torsional Restraints”.
The Deflection Limit Span Criteria must be specified, and is calculated independently for each span. For cantilevers, ‘L’ is taken to be twice the length of the cantilever.
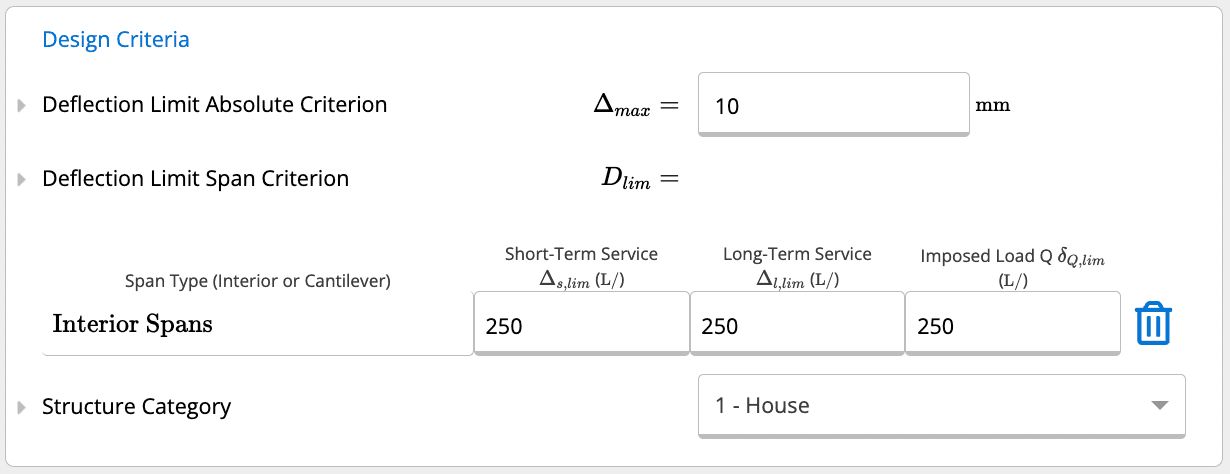
The Deflection Limit Absolute Criteria is the maximum deflection allowed, regardless of the span length.
These two deflection limit criteria are then used by the finite element solver to calculate the governing deflection limit, which is the minimum of the two:
![[SUPPORT]_how_to_design_a_timber_beam_to_as17201_2010_in_clearcalcs_au_7.png](https://cdn.prod.website-files.com/67189a2b26762b3b096e3184/673d7e7a0874de573c7e672e_SUPPORT_how_to_design_a_timber_beam_to_as17201_2010_in_clearcalcs_au_7_c8e5e7ee13.png)
Structure Category is used to determine the value of the capacity factor. You have to select from three categories: ‘House’, ‘Primary Structural Member’ and ‘Important Structure’. Explanation for the categories are provided in Table 2.1.
![[SUPPORT]_how_to_design_a_timber_beam_to_as17201_2010_in_clearcalcs_au_8.png](https://cdn.prod.website-files.com/67189a2b26762b3b096e3184/673d7e7b0874de573c7e675e_SUPPORT_how_to_design_a_timber_beam_to_as17201_2010_in_clearcalcs_au_8_effe4dd7da.png)
Position of the Supports from Left must be specified (see ‘How to Use the Beam Analysis Calculator’ for more detail). Where bearing calculations are not required for a particular support, the ‘Length of bearing’ cell may be set equal to zero. The values of the bearing factor, bearing capacity and governing reactions are automatically updated as supports and loading are changed.
![[SUPPORT]_how_to_design_a_timber_beam_to_as17201_2010_in_clearcalcs_au_9.png](https://cdn.prod.website-files.com/67189a2b26762b3b096e3184/673d7e7a0874de573c7e6735_SUPPORT_how_to_design_a_timber_beam_to_as17201_2010_in_clearcalcs_au_9_38d94577f6.png)
Input Loads
The input loads are split into ‘Permanent and Imposed Loads’ and ‘Wind and Other Loads’, which are then used to carry out a load case analysis. Loads can be input as distributed (patch) loads, line loads, point loads and moment loads. For distributed loads and line loads, it is important to specify the start and end location of the load in mm.
The self-weight of the beam is included as default; however, you can opt not to include this, by selecting ‘No’ from the drop-down menu next to Include Self-Weight.
You must then specify the Character of Imposed Load , so that the short-term, long-term and combination factors are then determined based on Table 4.1.
![[SUPPORT]_how_to_design_a_timber_beam_to_as17201_2010_in_clearcalcs_au_10.png](https://cdn.prod.website-files.com/67189a2b26762b3b096e3184/673d7e7b0874de573c7e67d0_SUPPORT_how_to_design_a_timber_beam_to_as17201_2010_in_clearcalcs_au_10_22422c30a5.png)
![[SUPPORT]_how_to_design_a_timber_beam_to_as17201_2010_in_clearcalcs_au_11.png](https://cdn.prod.website-files.com/67189a2b26762b3b096e3184/673d7e7b0874de573c7e6768_SUPPORT_how_to_design_a_timber_beam_to_as17201_2010_in_clearcalcs_au_11_d33549ca69.png)
ClearCalcs also enables load path tracking, meaning that reactions can be linked between beams and columns as point loads, by clicking the link icon next to the row of the load. More detail can be found in the article ‘Linking reactions between beams and columns (load path tracking) ’.
![[SUPPORT]_how_to_design_a_timber_beam_to_as17201_2010_in_clearcalcs_au_12.png](https://cdn.prod.website-files.com/67189a2b26762b3b096e3184/673d7e7b0874de573c7e6762_SUPPORT_how_to_design_a_timber_beam_to_as17201_2010_in_clearcalcs_au_12_3de7a95634.png)
Modification Factors
As listed in the assumptions, the Moisture Content when Fully Loaded and the Equilibrium Moisture Content (Annual Average) have been set to default values, which can be changed by typing into the input field or selecting from the drop-down menu. These are used to determine the Partial Seasoning factor k4.
![[SUPPORT]_how_to_design_a_timber_beam_to_as17201_2010_in_clearcalcs_au_13.png](https://cdn.prod.website-files.com/67189a2b26762b3b096e3184/673d7e7b0874de573c7e676b_SUPPORT_how_to_design_a_timber_beam_to_as17201_2010_in_clearcalcs_au_13_d3fcdb0845.png)
The Temperature Factor k6, is generally taken to be 1 unless seasoned timber is used in coastal regions in the north of Queensland at latitude 25oS, and all regions north of latitude 16oS, where 0.9 is used.
The Number of Discrete Parallel Members must be input, as shown in the example below. It is assumed that two parallel members do not constitute a discrete parallel system, and more than 10 do not have additional benefit.
This is then used to calculate the Strength Sharing Factor k9.
![[SUPPORT]_how_to_design_a_timber_beam_to_as17201_2010_in_clearcalcs_au_14.png](https://cdn.prod.website-files.com/67189a2b26762b3b096e3184/673d7e7b0874de573c7e67c2_SUPPORT_how_to_design_a_timber_beam_to_as17201_2010_in_clearcalcs_au_14_1114e41753.png)
Summary Outputs
The maximum moment, shear and bearing demands are shown, along with the capacities and the percentage utilised. The actual serviceability deflections and governing limits are also shown. These are determined by the ClearCalcs finite element analysis engine.
The shear, bending moment and deflection diagrams are also shown and you can select which load case to display graphically, by selected from the drop-down Graphed Load Case menu. A diagram of the loading and reactions is also displayed.
![[SUPPORT]_how_to_design_a_timber_beam_to_as17201_2010_in_clearcalcs_au_15.png](https://cdn.prod.website-files.com/67189a2b26762b3b096e3184/673d7e7a0874de573c7e673b_SUPPORT_how_to_design_a_timber_beam_to_as17201_2010_in_clearcalcs_au_15_12a7b8ba7f.png)
References
- AS1720.1:2010 – Timber Structures
- AS1684.2:2010 – Residential Timber-Framed Construction: Non-cyclonic Areas
- AS1170.0:2002 – Structural Design Actions: General Principles
- AS1170.1:2002 – Structural Design Actions: Permanent, imposed and other actions
- AS1170.2:2011 – Structural Design Action: Wind actions