Timber bolted connections, are commonly used in timber structures, from residential to larger commercial applications, because they allow for efficient load transfer between members and flexibility during assembly.
The main benefits of timber bolted connectors are:
- High load-carrying capacity
- Ease of assembly and disassembly
- Durability and reliability
- Versatility in applications (can be applied at angles)
- Compatibility with engineered wood products
- Reduced splitting risk
- Performance under cyclic and dynamic loads
- Cost-effectiveness
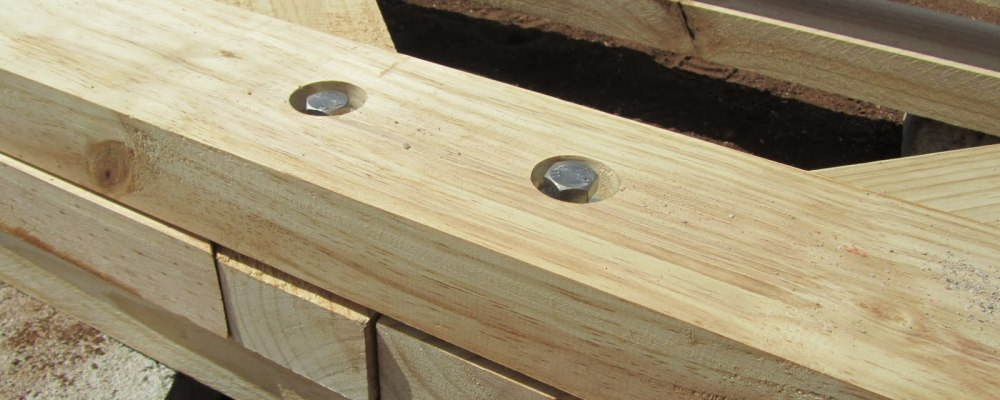
This guide is a resource for structural engineers. It covers the fundamentals of Australian standards AS 1720.1, its scope, and the key design parameters for timber bolted connections.
Note: This design guide is intended to be informative, but compliance with AS 1720.1(2010) design standards must be ensured in every design. The designer must have the appropriate qualifications depending on the jurisdiction in which they are designing.
AS 1720.1 Timber Structures
AS 1720.1 provides structural design methods for timber and engineered wood products used in building construction. It covers:
- Structural design principles for timber and wood-based materials.
- Requirements for designing connections, including bolted, nailed, and screwed timber joints.
- Load-carrying capacity criteria for connections subjected to various loads.
- Provisions for different timber species, moisture conditions, and service environments.
- The standard applies to all types of solid timber, including softwood and hardwood, as well as engineered wood products such as plywood, laminated veneer lumber (LVL), and glued laminated timber (glulam). Specifically, AS1720.1 provides guidelines for joint types, spacing, and bolt sizes to achieve optimal performance for timber connectors, such as bolted connections.
In this article, we will cover the design procedure for timber bolted connections in accordance with AS 1720.1(2010) Timber Structures.
Design parameters
Timber properties
- Joint group: Joint groups categorize timber species based on their density, hardness, and connection performance. The performance is primarily focused on the timber's capacity to hold fasteners like nails, bolts, or screws under loading conditions. The Joint groups used in AS 1720.1:2010 include the following:
- JD1 to JD6: Used for seasoned (dry) timber.
- JD1 is the strongest, usually representing high-density, seasoned hardwoods.
- JD6 is the weakest, usually for lower-density, seasoned softwoods.
- J1 to J6: Used for unseasoned (green) timber.
- J1 is the strongest, usually high-density, unseasoned hardwoods.
- J6 is the weakest, usually low-density, unseasoned softwoods.
- JD1 to JD6: Used for seasoned (dry) timber.
- Grain direction: The strength of timber varies depending on loading parallel or perpendicular to the grain, influencing the design of bolted connections.
Bolted connection types
- Single shear and double shear connections: Bolted timber joints can either be single shear (two connected members) or double shear (three connected members). AS 1720.1 provides formulas and factors for each connection type.
- Spacing and edge distances: The standard specifies the minimum spacing between bolts and from the edge of timber members to avoid splitting and ensure load distribution.
- Bolt size: Bolts must meet minimum size requirements based on load and timber type. Common bolt diameters in timber design range from 10mm to 24mm.
Load conditions
- Axial load: Loads acting along the member's length. Bolted connections in axial loading are typically less demanding than those under perpendicular load.
- Lateral load: Loads acting perpendicular to the timber member. Lateral loads significantly impact bolted connections due to potential shear forces on bolts.
- Combined loads: When axial and lateral loads are combined, AS 1720.1 provides interaction equations to ensure the connection can safely support both loads simultaneously.
Connection detailing
- End and edge distances: AS 1720.1 specifies minimum distances from the bolt center to the end or edge of timber members to prevent splitting.
- Bolt spacing: Minimum and maximum spacing between bolts is critical to ensure even load distribution across the connection. Excessive spacing can cause uneven loading, while tight spacing may reduce load-carrying capacity.
- Number of bolts: The standard outlines the maximum allowable number of bolts in a connection, balancing load distribution and timber’s splitting resistance.
Service factors and duration of load
AS 1720.1 adjusts the design capacity based on load duration, with different factors for permanent, short-term, and instantaneous loads. These adjustments ensure the connection’s longevity.
Exposure conditions, including weathering and potential decay in untreated timber, are accounted for with adjustment factors. For example, an outdoor bolted connection may require corrosion-resistant bolts and larger safety factors.
Safety and capacity factors
AS 1720.1 uses safety factors to account for uncertainties in material properties and construction variability. Typical factors range between 0.6 and 0.9 for timber bolted connections.
Design procedure
Step 1: Determine characteristic capacity of bolts
As per Clause 4.4.2.4 of AS 1720.1, the characteristic capacity for a laterally loaded single bolt in a bolted joint system (Qsk) shall be derived as follows:
a) For systems loaded parallel to grain:
$$Q_{sk}=Q_{sk1}$$
Where
$$Q_{sk1}\text{ is given in Table 4.9(A) of AS 1720.1}$$
b) For systems loaded perpendicular to the grain:
$$Q_{sk}=Q_{skp}$$
Where
$$Q_{skp}\text{ iis given in Table 4.10(A) of AS1720.1}$$
c) For systems loaded at an angle to the grain, (θ):
$$Qsk=\frac{Q_{sk1}Q_{skp}}{Q_{sk1}sin^2(\theta)+Q_{skp}cos^2(\theta)}$$
The system capacity parameters are determined from AS 1720.1(2010) Table 4.9(B-C) and Table 4.10 (B-C).
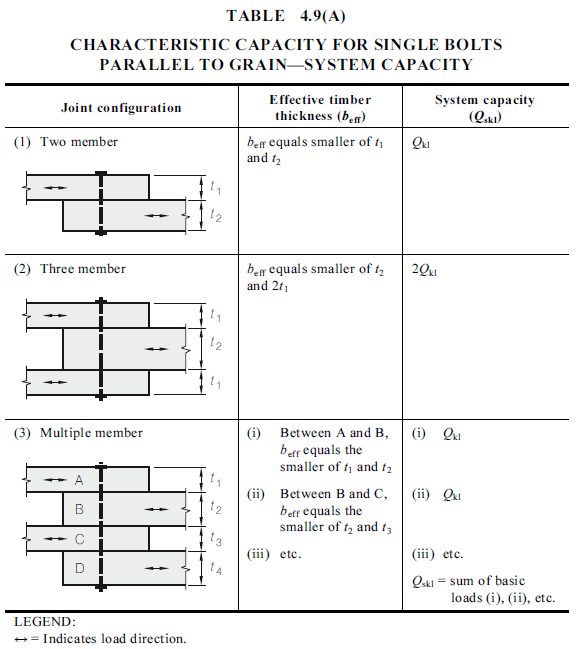
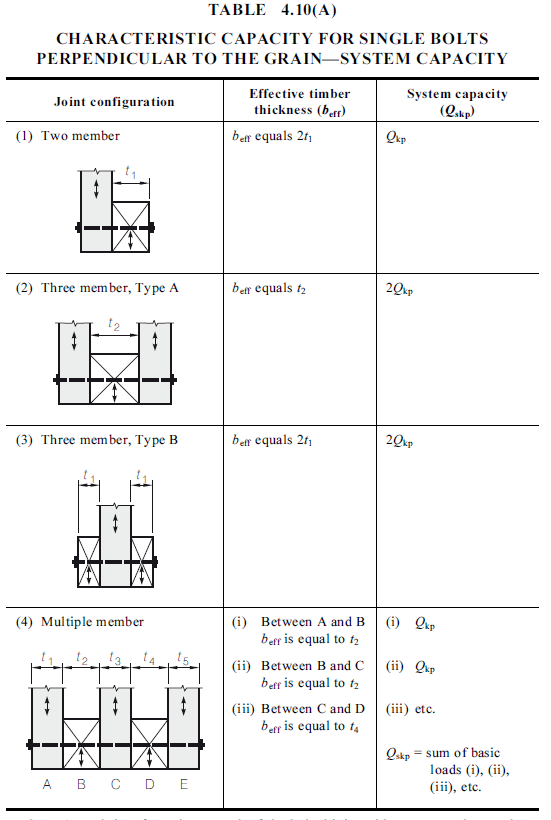
The maximum tensile load capacity for a bolt subject to direct axial loading shall not exceed the value appropriate to the diameter and metal from which the bolt is manufactured, as given in AS 1720.1(2010) Table 4.11.

Step 2: Determine joint type
There are two joint types:
- Type 1 joint where fasteners subject to shear loads where the fastener is into the side or end grain of connected members
- Type 2 joint where fasteners subject to axial loads where the fastener is installed into the side or end grain of connected members
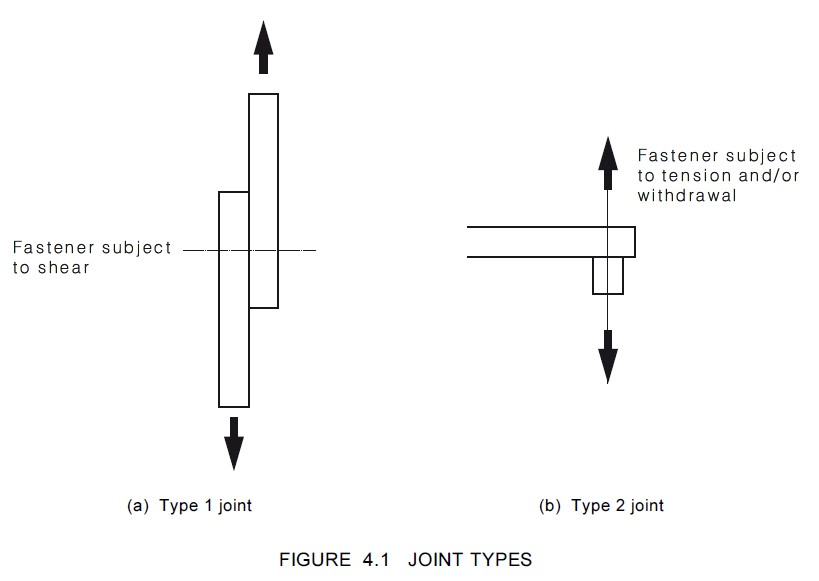
Step 3: Determine design capacity of Bolted Connection
Type 1 Joint
The design capacity (Nd,j) for a Type 1 joint containing n bolts in shear to resist lateral loads, as illustrated in AS 1720.1 (2010) Table 4.9 and Table 4.10, shall satisfy the following.
$$N_{d,j}\ge N^*$$
$$N_{d,j}=\theta k_1k_{16}k_{17}nQ_{sk}$$
Where
$\theta$= capacity factor (Clause 2.3 AS1720.1(2010)), 0.6 is most conservative
$k_1$= the factor for duration of load for joints (Clause 2.4.1.1 AS1720.1(2010)), 0.57 is most conservative
$k_{16}$= 1.2 for bolts that transfer load through close fitting holes into metal side plates, 1.0 otherwise
$k_{17}$= factor for multiple bolted joint given in Table 4.12 AS1720.1(2010) shown below
$n$= total number of bolts in connection resisting design action effect in shear
$Q_{sk}$= characteristic capacity as per Step 1 above
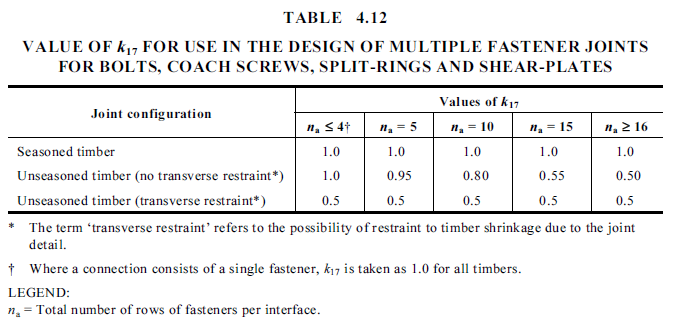
3.3.1 Type 2 Joint
The design capacity (Nd,j) for a Type 2 joint in which bolts are loaded in direct tension shall satisfy
$$N_{d,j}\ge N^*$$
Where
$$N_{dj}=nN_{d,tb}$$
$$N_{d,j}=\theta k_1k_7nf'_{pj}A_w$$
$N^*$= design action effect in direct tension
$n$= total number of bolts in connection resisting design action effect in shear
$N_{d,tb}$= design capacity of bolt in tension as per Table 4.11 in AS 1720.1(2010)
$\theta$= capacity factor (Clause 2.3 AS1720.1(2010)), 0.6 is most conservative
$k_1$= the factor for duration of load for joints (Clause 2.4.1.1 AS 1720.1(2010)), 0.57 is most conservative
$k_7$= length of bearing factor as per Table 2.6 AS 1720.1(2010)
$f'_{pj}$= characteristic bearing capacity for timber in joints as per AS 1720.1(2010) Table C6
$A_w$= effective area of washer for bearing as per AS 1720.1(2010) Table 4.11
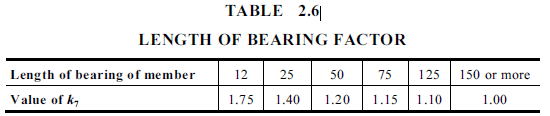
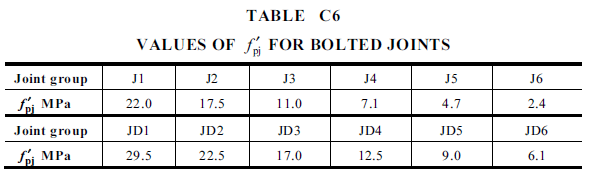
Bolted joints with loads at an angle to the bolt axis
As per AS 1720.1(2010) Clause 4.4.3.4, the design capacity (Ndj) for a joint in which bolts are loaded at an angle to the axis of the bolts (see Figure 4.8) shall satisfy:
- AS 1720.1(2010) Clause 4.4.3.2, which is the Type 1 Joint criteria captured above for that component of the load normal to the bolt axis; and
- AS 1720.1(2010) Clause 4.4.3.3 which is the Type 2 Joint criteria captured above for that component parallel to the bolt axis.
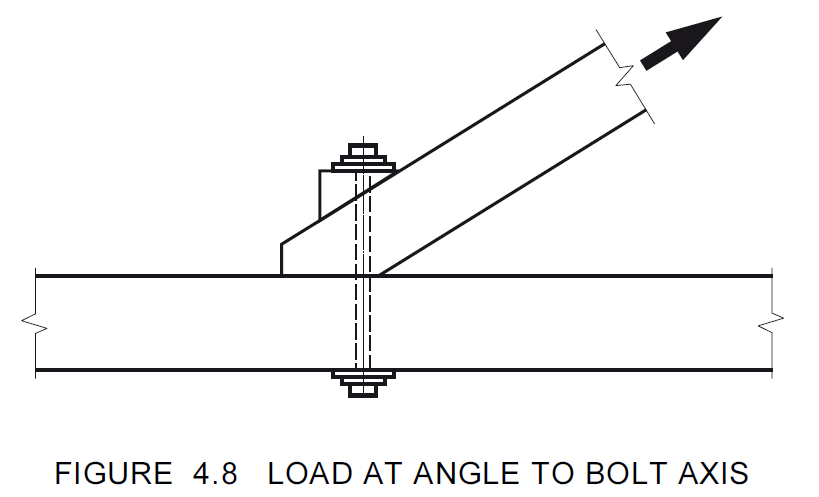
Step 4: Specify spacings, edge and end distances for bolts
As per AS 1720.1(2010) Clause 4.4.4, the edge, end and between-fastener spacings are not less than those shown in Figure 4.9.
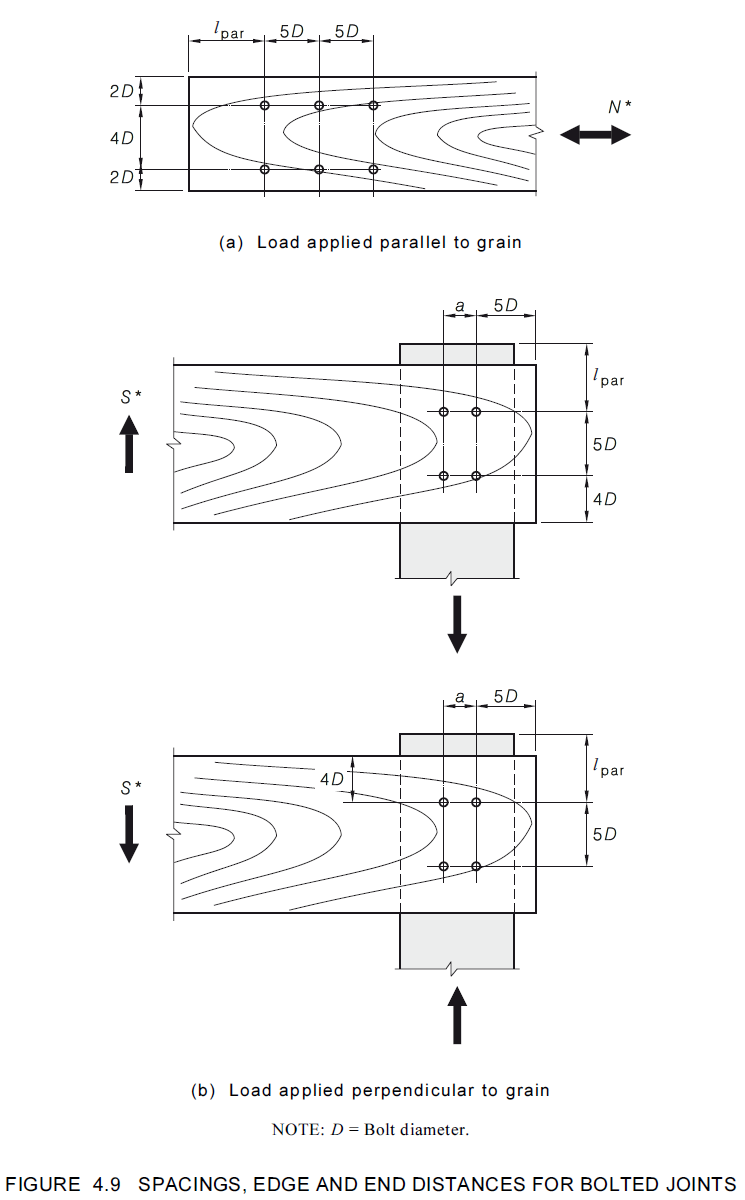
End Distance (lpar)
As per AS 1720.1(2010) Clause 4.4.4.2, the required end distance (lpar) shall be at least 8D in tension joints in unseasoned timber, 7D in tension joints in seasoned timber, and 5D in compression joints and in joints subject to bending moment for both moisture conditions.
It is appropriate to use lesser end distances in tension joints provided the characteristic capacity is reduced in proportion to the reduction in end distance.
In no case shall the end distance for tension joints be less than 6D for unseasoned timber and 5D for seasoned timber
Spacing between bolts perpendicular to load (a)
As per AS 1720.1(2010) Clause 4.4.4.3, the distance, a, shall be at least 2.5D for a b/D ratio of 2, and it shall be increased proportionately so that it is at least 5D for a b/D ratio of 6 or more, where b is the effective thickness of the member loaded perpendicular to the grain.
Loads acting at an angle to the grain
As per AS 1720.1(2010) Clause 4.4.4.4, for loads acting at an angle 0° to 30° to the grain, the spacings, edge and end distances shall be taken as for loads parallel to the grain. For loads acting at an angle of 30° to 90° to the grain, the spacings, edge and end distances shall be taken as for loads acting perpendicular to the grain.
Step 5: Specify washers
As per AS 1720.1(2010) Clause 4.4.5, in all timber-to-timber bolted structural joints, every bolt shall be fitted with a washer at each end, of a size not less than that given in Table 4.11 which is shown in Step 1.
Step 6: Eccentric joints
As per AS 1720.1(2010) Clause 4.4.6, when it is impracticable to ensure that all the members meeting at a joint (see Figure 4.9 in Step 4) are arranged symmetrically, that is, the members’ centroidal axes intersecting on a common axis which is also the axis of resistance of the bolt or group of bolts, then the combination of primary stresses (induced by axial loads) and secondary stresses (induced by bending moment resulting from bolt eccentricities) shall be checked to ensure that no member or fastener is excessively stressed.
In addition, the design capacity in transverse shear at an eccentric joint (Vd,sj) shall satisfy the following:
$$V_{d,sj}\ge V^*_{sj}$$
$$V_{d,sj}\ge \theta k_1k_4k_6f_{sj}'A_{sj}$$
Where
$V^*_{sj}$= design action effect in shear on the joint
$\theta$= capacity factor (see Clause 2.3)
$k_1$= the factor for duration of load for joints (Clause 2.4.1.1 AS1720.1(2010)), 0.57 is most conservative
$k_4$= length of bearing factor as per Table 2.6 AS1720.1(2010)
$k_6$= 1.0 (0.9 if coastal Queensland or northern Australia) as per Clause 2.4.3 of AS1720.1(2010)
$f_{sj}'$= characteristic value in shear at joint details appropriate to species strength group
$A_{sj}$=$\frac{2bd_s}{3}$ (see Figure 4.10 from AS1170.1(2010)
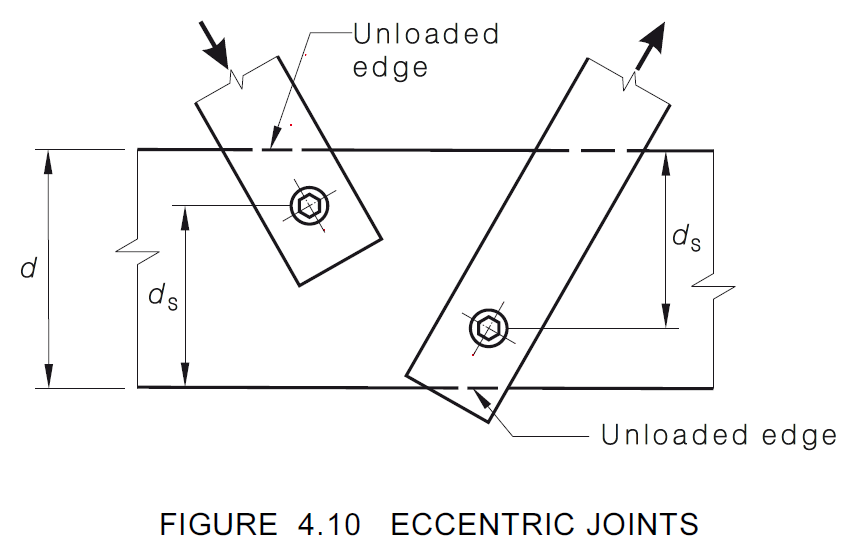
Timber bolted connection design by hand calculation
Design a timber bolted connection that will connect two 90x45 JD2 species timbers together with the load applied parallel to the grain. The bolted joint is for a timber residential building and is subjected to a shear load of 2kN (dead load). The live loads consist of 1 kN shear in the same direction as the dead load.
Step 1: Determine characteristic capacity of bolts
As per Clause 4.4.2.4 of AS 1720.1, the characteristic capacity for a laterally loaded single bolt in a bolted joint system (Qsk) shall be derived as follows:
For systems loaded parallel to grain for M6 bolts (which we will try first as they are smallest/cheapest available):
$Q_{sk}=Q_{sk1}=Q_{k1}$= 3500N for a two member joint configuration as per Table 4.9(A) & 4.9(C) of AS1720.1
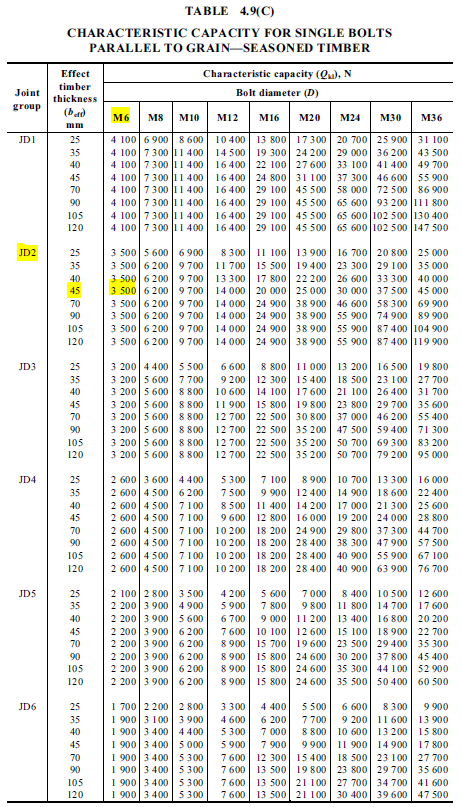
The maximum tensile load capacity for a bolt subject to direct axial loading shall not exceed the value appropriate to the diameter and metal from which the bolt is manufactured, as given in AS 1720.1 (2010) Table 4.11, which is 6400N for M6 bolts.
This provides us with a round washer size of 30mm with a thickness of 1.6mm and an effective bearing area (Aw) of 200 mm2.
Step 2: Determine joint type
There are two joint types:
- Type 1 joint where fasteners subject to shear loads where the fastener is into the side or end grain of connected members
- Type 2 joint where fasteners subject to axial loads where the fastener is installed into the side or end grain of connected members
In this problem, the joint is a type 1 joint as we only have shear force.
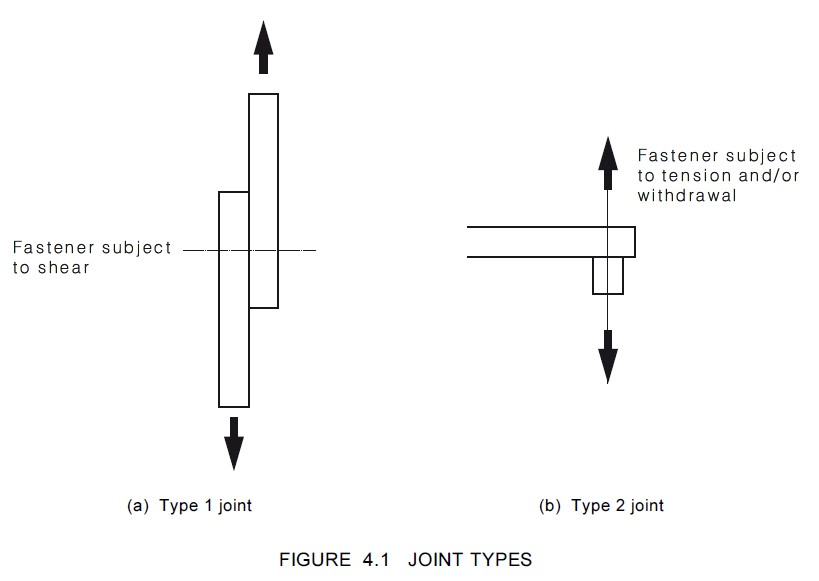
Step 3: Determine design capacity of bolted connection
The design capacity (Nd,j) for a Type 1 joint containing n bolts in shear to resist lateral loads, as illustrated in AS 1720.1 (2010) Table 4.9 and Table 4.10, shall satisfy the following.
$$N_{d,j}\ge N^*$$
$$N_{d,j}=\theta k_1k_{16}k_{17}nQ_{sk}$$
$$N^*=1.2G+1.5Q=1.2(2)+1.5(1)=3.9kN=3900N$$
Where
$\theta$= capacity factor (Clause 2.3 AS 1720.1(2010)), 0.6 is most conservative
$k_1$= the factor for duration of load for joints (Clause 2.4.1.1 AS 1720.1(2010)), 0.57 is most conservative
$k_{16}$= 1.2 for bolts that transfer load through close fitting holes into metal side plates, 1.0 otherwise}
$k_{17}$= 1.0 (factor for multiple bolted joint given in Table 4.12 AS 1720.1(2010) - try 4 bolts)}
$n$= total number of bolts in connection resisting design action effect in shear
$Q_{sk}$= 3500N (characteristic capacity as per Step 1 above)
Therefore, the number of M6 bolts required is given by:
$$n\ge \frac{N^*}{\theta k_1k_{16}k_{17}Q_{sk}}=\frac{3900}{0.6*0.57*1.0*3500}=\text{3.25 bolts}$$
Therefore, we will use 4 M6 bolts.
Step 4: Specify spacings, edge and end distances for bolts
As per AS 1720.1(2010) Clause 4.4.4, the edge, end and between-fastener spacings are not less than those shown in Figure 4.9.
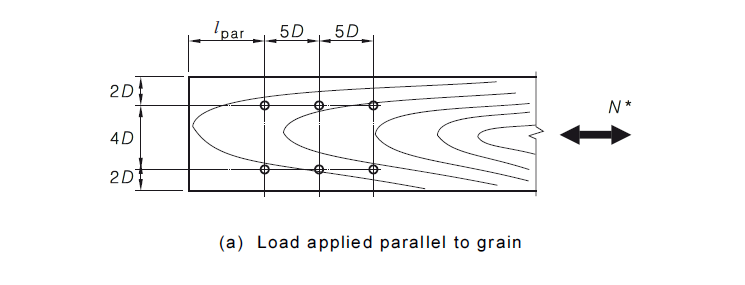
End Distance (lpar)
AS 1720.1(2010) Clause 4.4.4.2 recommends an end distance of at least 7D for seasoned timber, which for M6 bolts gives an end distance of 42mm. It is possible to go down to 5D for this problem, but let’s be conservative.
Spacing between bolts perpendicular to load (a)
Our bolt diameter D is 6mm. Our member width (b) is 45mm. Our b/D ratio is 9.
As per AS 1720.1(2010) Clause 4.4.4.3, the distance, a, shall be at least 5D for a b/D ratio of 6 or more.
Therefore, our spacing between bolts (a) will be 30mm.
Step 5: Specify washers
As per AS 1720.1(2010) Clause 4.4.5, in all timber-to-timber bolted structural joints, every bolt shall be fitted with a washer at each end, of a size not less than that given in Table 4.11, which is shown in Section 3.1 of this guide.
For M6 bolts, round washers must be minimum 30mm in diameter and 1.6mm in thickness.
Timber bolted connection design using ClearCalcs
ClearCalcs allows engineers to assess different fastening methods, including bolted joints, nail plates, and other hardware solutions.
Design a timber bolted connection that will connect two 90x45 J2 species timbers together with the load applied parallel to the grain. The bolted joint is for a timber residential building and is subjected to a shear load of 2kN (dead load). The live loads consist of 1 kN shear in the same direction as the dead load.
Step 1: Populate the applied design loads
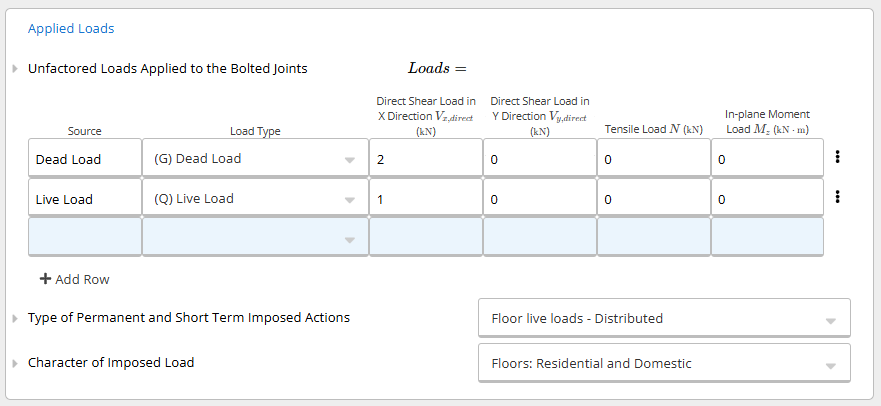
Step 2: Fill in the known design parameters
Next, under the key properties section, detail the known parameters, such as the species group (J2), effective thickness (90mm as double the thickness of the connected members as per AS 1720.1 (2010) Table 4.9(A)), grain parallel to the load direction (0 degrees), in a residential building (category 1), that has no strengthening or transverse restraint.

Step 3: Iterate bolt patterns and sizes to find a conforming design
Next, trial M6 bolts (the smallest and cheapest bolts) with a bolt pattern that fits in with the dimensions of the two connected member widths.
If it is not possible to reasonably fit in a bolt arrangement within the width of the connected members, the bolt size should be increased until an arrangement can be found. It’s best to discuss the proposed bolt arrangement with the builder to ensure it is constructible.
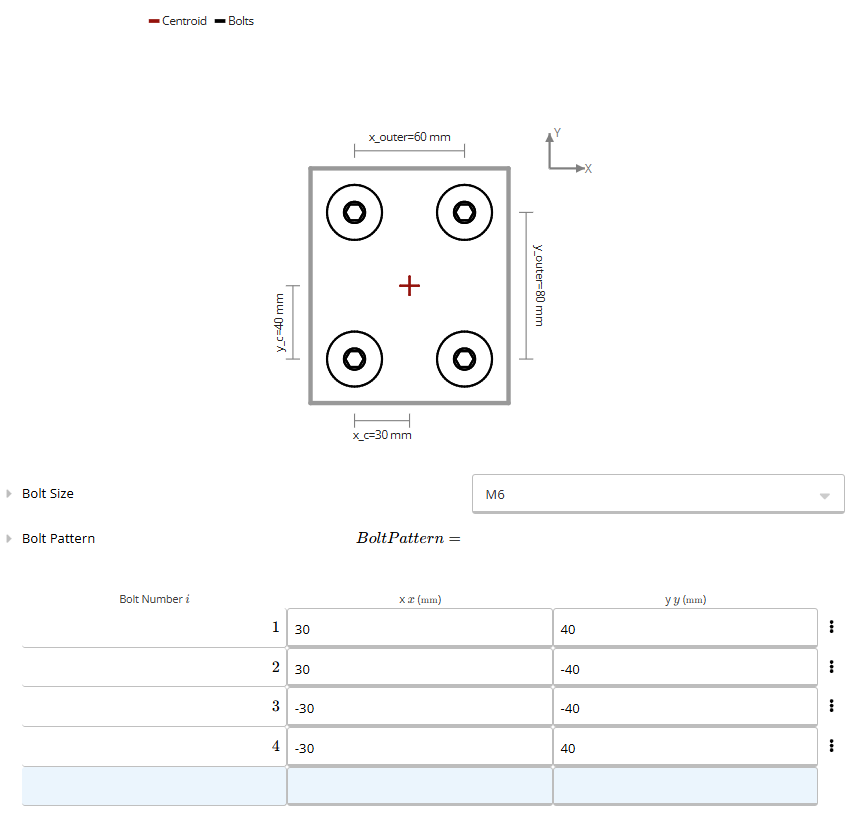
The key is to ensure that the utilisation of the shear and tensile capacity remains below 100%. A good target for load utilisation is 80% as it nicely balances a factor of safety with a structurally efficient design. It can be useful in this step to ask what size bolts they have in stock, because an arrangement may be able to be found for those bolts which is a great way to deliver value for your client.
By ClearCalcs providing instantaneous feedback for the load utilisation of different bolt arrangements, designers can find the most efficient solution or provided a number of compliant solutions to their customer to ease constructability on site.
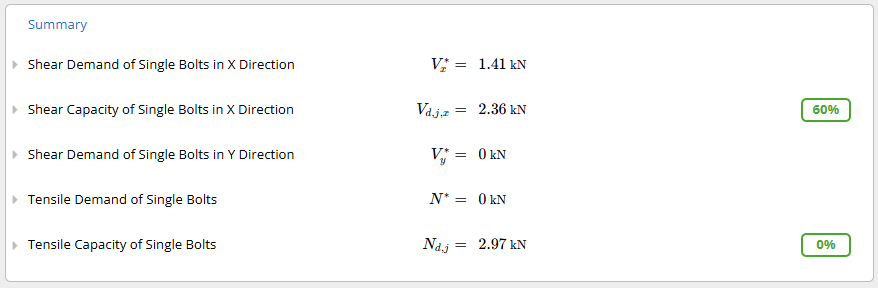
Step 4: Specify washer size, type and edge distance
The washers chosen depend on the size of the bolts used. Table 4.11 from AS 1720.1(2010) should be referred to for determining the appropriate washer size. In this instance, for M6 bolts a 30mm round washer has been chosen. Again, the builder may have a certain washer size in stock so check with them as they may have a preference for a larger size which could be used.
The distance between the washer and the nearest edge will depend on the member dimensions. In this case the members depth is 90mm, so with two bolts spaced 30mm apart will leave the distance to the edge of the nearest washer at 30mm.

Step 5: Export your calculation to append to your design
Many jurisdictions require the engineer to provide detailed calculations to meet regulatory compliance. Some clients even specify this as a requirement of the design. ClearCalcs automatically exports the calculations completed in the background in accordance with AS 1720.1(2010) to save you time and ensure there are no calculation errors.
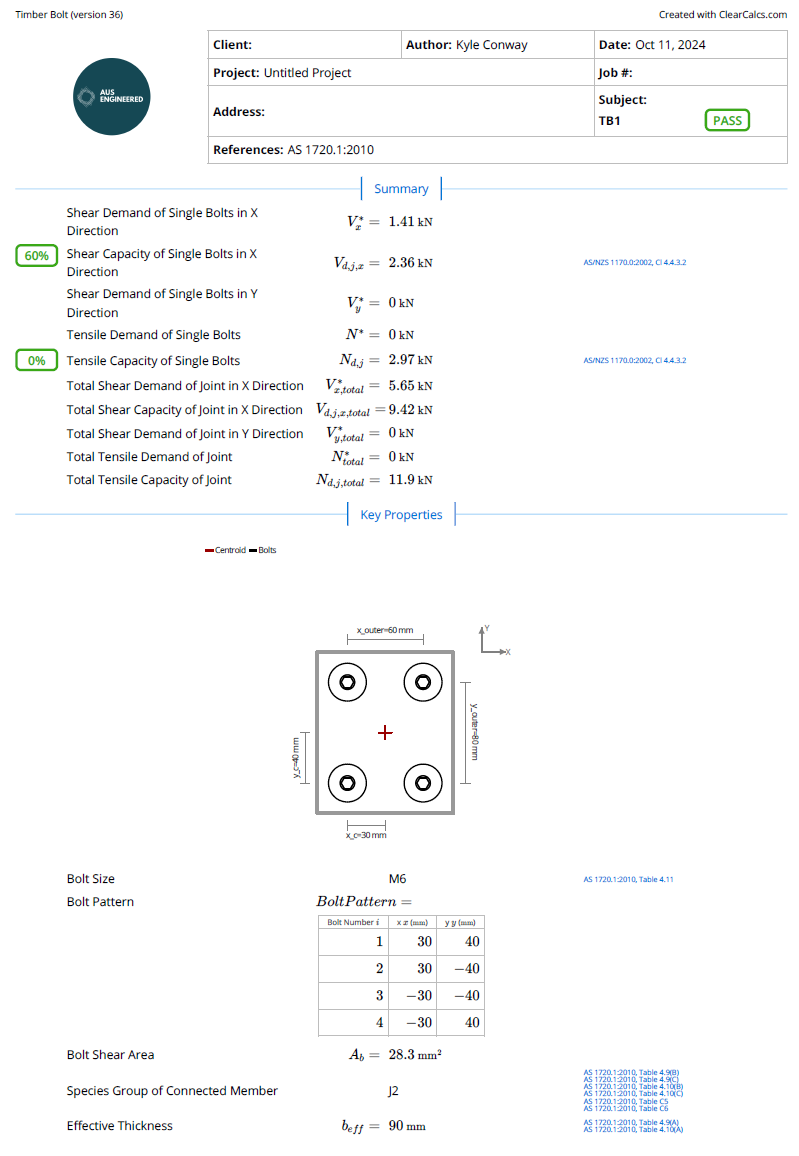
Conclusion
This guide to designing timber bolted connections according to AS 1720.1 (2010) covers essential parameters, design examples by hand and using ClearCalcs for safe and efficient structural timber design.
By adhering to AS 1720.1 guidelines and relevant legislation to the jurisdiction you are designing, engineers can ensure that timber construction meets performance and safety requirements in various loading and environmental conditions.
ClearCalcs can greatly speed up the timber connections design process leading to faster, more efficient designs, delivering better results for your organisation and the end client.
ClearCalcs ensures your calculations are compliant with standards, and the calculators get updated as standards get revised by the governing authority, meaning your design will always be checked for compliance against the appropriate building codes without you needing to adjust your procedure.
Start your free trial today.
Seismic Retrofit Series: URM Insights for US and Canada Engineers
August 5th at 1 pm Eastern Time (ET)
Save your spot →